Thermodynamics and safety (2)
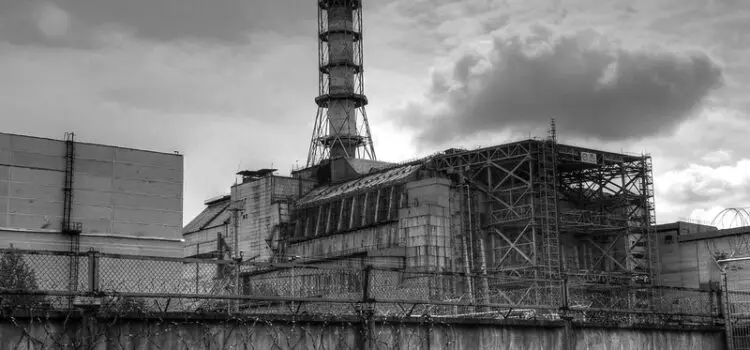
Technological systems in the real world are either based on or heavily influenced by the laws of thermodynamics and technical thermodynamics. Examples include thermal engines (i.e. all combustion engines), heat pumps, refrigerators, air conditioning, and cooled electronic components mentioned in the first part of the article (1). It is clear that some critical technologies or processes in practice are very vulnerable from a thermodynamic perspective, meaning they are sensitive to thermodynamic events (e.g., sensitive to changes in ambient temperature, dependent on cooling, sensitive to changes in pressure, etc.). Changes in certain thermodynamic parameters may trigger thermodynamic reactions or other dangerous behaviors that threaten or directly damage the surrounding environment, other systems, the living environment, and even the human system, health, and lives of people. These events, which lead to significant losses in public assets such as people’s and companies’ property, the environment, and human lives and health, are called extreme phenomena.
Some extremes that play a great role in thermodynamics are shown in the following examples.
Tanks and transport tanks of liquefied gases
For the description of the properties of liquefied gas storage tanks and transport tankers, we base our work on (J. HORÁK) dealing with the use of thermodynamic data to assess the potential hazard of liquefied gas storage tanks 1.
An extreme event in this case can be considered the leakage of the contents of storage tanks and tankers, primarily used in the chemical and petrochemical industries. Most liquefied gases have hazardous properties, some are toxic or corrosive, e.g., chlorine, hydrogen chloride, sulfur dioxide, ammonia, hydrogen sulfide, phosgene, others are flammable, e.g., ammonia, propane, propene, butane, butadiene, and vinyl chloride, and therefore, in the event of an accident, they can cause significant damage to the environment and also to human health and lives.
These storage tanks and tankers can therefore be considered dangerous means that, in the event of an accident, can cause:
- leakage of a large amount of hazardous substance,
- formation of a mixture of hazardous gas and air,
- in the case of toxic gas, i.e. toxic cloud threatening the population and the environment,
- in the case of flammable gas, i.e. flammable cloud which, under certain conditions, may ignite and create a “fireball” threatening with heat radiation,
- in the case of explosive substance, gas cloud which can threaten the surroundings with its explosion, destructive wave, and heat radiation.
The cited work 2 uses the following important terms for the analysis of selected accident scenarios:
- Adiabatic boiling – to occur, liquefied gas must be heated above its normal boiling point. Upon pressure release, a so-called “flash boiling” occurs, where phase change uses the internal heat of the liquefied gas, with no delay caused by heat absorption from the surroundings,
- Boiling controlled by heat transfer to the liquid – liquefied gases have a boiling point lower than the ambient temperature. Therefore, at atmospheric pressure, they boil, with the rate of evaporation being limited by the heat transfer rate from the surroundings to the liquid.
Accident scenarios for storage tanks divide the work space into two parts: the liquid space filled with liquefied gas and the gas part filled with compressed gas. Leakage scenarios are divided into leakage from the liquid space and leakage from the gas space. In both cases, “slow” and “fast” leakage of gas or liquid from the leakage holes of the liquid or gas space are considered.
- Fast leakage is accompanied by adiabatic boiling, leading to the destructive effect of the expansion energy of the vapor, causing the liquid to be dispersed in droplets into the gas space, accelerating the boiling process. There is also spraying of the liquid in the form of foam. The leakage rate depends on the parameters of the leakage path of the gas and whether the leakage path is connected to the liquid and gas parts. For an emergency leakage, the work assumes a fast leakage.
- Slow leakage is accompanied by boiling controlled by heat transfer to the liquid, where no liquid leakage occurs, only compressed gas is involved, “and the destructive effect of the expansion energy of the vapor is not significantly applied.” An example of slow leakage is when using pressure cylinders with a propane-butane mixture for cooking in households.
“In the analysis of scenarios, the case where the tank is ruptured by the pressure of the vapor is not included. Rupture occurs in extreme situations, e.g., during a fire, when the contents of the tank are heated to a high temperature. This case is referred to as a physical explosion” 3.
The cited work considers the following characteristics necessary to obtain relevant results:
- pressure in the tank,
- ratio of the largest retention in the tank to the smallest retention,
- for the gas space – estimation of the mass of the retention released from the steam space of the tank when the pressure is released,
- for the liquid space – overheating of the liquid above the normal boiling point,
- for the liquid space – the portion of the liquid that can evaporate by adiabatic boiling.
For the analysis of the potential hazard of a leak, it is necessary to calculate the expansion work of the steam in the gas space and the steam generated by boiling.
- Expansion work provides basic information about the intensity with which the vapor can escape. For calculation, relationships derived for adiabatic expansion can be used. “During adiabatic expansion, the vapor does work at the expense of its internal energy, and therefore, the vapor cools down, and the equality holds:” expansion work of the vapor is equal to the decrease in internal energy of the vapor. Two limiting values of expansion work are useful:
- Expansion work of the vapor during reversible adiabatic expansion (maximum expansion work),
- Expansion work of the vapor during irreversible adiabatic expansion against ambient (atmospheric) pressure (minimum necessary work).
- The difference between the maximum and minimum necessary work is called unbound work, which typically transforms into another form of dangerous energy – e.g., destructive shockwave, dispersing energy spreading the liquid into fine droplets or into kinetic energy of the flowing liquid and gas stream. This unbound work then affects the mixing rate of the vapor or the liquid-vapor mixture with the air and significantly influences the formation of the escaped substance cloud. The transformation of this energy part depends on the process speed. In the case of slow leakage, it may remain untransformed as the visible heat of the vapor.
Work generated by boiling includes: volumetric work of the vapor associated with the expansion of the vapor in the gas space of the tank; expansion work of the vapor generated by irreversible adiabatic boiling of the liquid.
The basic design parameter (according to the cited work 4) that affects the severity of the consequences of an accident is the volume and retention of hazardous substance in it. By organizing processes, the volume of storage tanks and retention can be reduced, but in practice, poor organization often forces the construction of large storage tanks and maintaining large retention.
The most important technological parameter is the difference between the storage temperature and the normal boiling point, because the energy accumulated as overheating of the contents above the normal boiling point represents a hazardous form of energy, which is then transformed into evaporative heat and expansion work. Reducing this temperature difference means introducing additional cooling equipment, which carries other risks; therefore, cooling must be handled specifically for each type of tank. Furthermore, according to the accident progression analysis, the fast phase, where the liquid is pushed out of the tank by vapor pressure, is more dangerous. Therefore, in the case of an accident (or leak), it is advisable to reduce the pressure in the tank by controlled venting of the vapor. “In the form of overheating, relatively large amounts of energy are accumulated, but the decisive part is transformed into evaporative heat, and only a very small portion may manifest as expansion work causing destruction. The main source of potential hazard of the tanks is thus their ability to release large amounts of vapor into the environment and create a hazardous substance cloud.”
Finally, to illustrate the importance of thermodynamics in reservoirs in safety, we can recommend the following video and document:
Thermodynamics of the steam cycle of nuclear power plants - nuclear accident
For the description of extreme phenomena caused by nuclear reactions, further details are not necessary, as the most well-known events in nuclear energy and wartime conflicts worldwide, including in Czechoslovakia, can be referred to:
The atomic bombing of the cities of Hiroshima and Nagasaki in Japan in 1945,
The nuclear accident at Jaslovské Bohunice A-1 in 1976 and 1977,
The Three Mile Island nuclear accident in the USA in 1979,
The severe nuclear accident at Chernobyl in Ukraine in 1986,
The very severe Fukushima nuclear accident in Japan in 2011.
The following sections are based on the bachelor’s thesis by (T. KOZÁK) 5, which does not describe extreme events, but contains a description of the steam cycle of nuclear power plants from a thermodynamic perspective and an overview of the types of nuclear reactors and their constructions. Based on this work, the importance of thermodynamics in nuclear energy is demonstrated, as external influences, as well as internal organizational and technological failures, can disrupt the thermodynamic cycle of the power plant, leading to extreme phenomena, i.e., failures, and more or less severe nuclear accidents.
The cited work provides a brief introduction and history of nuclear research and energy, followed by an introduction to thermodynamics, i.e., heat cycles, the Carnot cycle, and thermodynamics of steam (see thermodynamic laws and cyclic processes). In the second part, it describes the ideal and real Rankine-Clausius steam cycle, the increase in thermal efficiency, and the Carnotization of the cycle.
The Ideal Rankine-Clausius Cycle changes the energy accumulated in steam into mechanical work. It consists of four thermodynamic processes or states shown in the diagram, with the course of these processes plotted on the T-s diagram of water and steam.
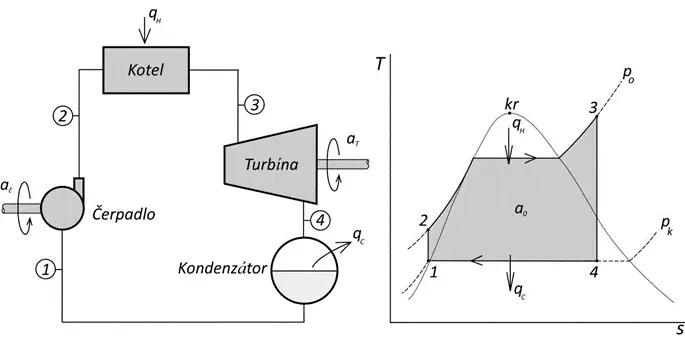
Process 1-2: Adiabatic Compression, i.e., an increase in temperature of saturated liquid by pressure.
Process 2-3: Isobaric Heating; the liquid is heated in the boiler (steam generator, reactor) at constant pressure and is converted into saturated or superheated steam.
Process 3-4: Adiabatic Expansion; i.e., the steam expands through the turbine, converting its energy into work (rotation of the turbine).
Process 4-1: Condensation; i.e., the steam condenses back into saturated liquid.
The ideal heat cycle neglects losses that directly affect the decrease in thermal efficiency. These primarily include thermal losses and pressure losses in the boiler and condenser, as well as irreversible processes occurring in the turbine and pump.
Real Rankine-Clausius Cycle – “The most significant decrease in thermal efficiency of the cycle is caused by irreversible processes that occur when the steam passes through the turbine. In the case of the ideal cycle, we assume that expansion in the turbine is isentropic, which corresponds to the appropriate thermal drop (the difference in enthalpies of the steam at the turbine’s inlet and outlet). However, when the steam passes through the turbine, expansion losses occur, and as a result, the expansion curve deviates in the direction of increasing entropy. The enthalpy of the steam leaving the turbine is higher than in the case of ideal isentropic expansion. Therefore, this reduces the actual thermal drop, which means a decrease in turbine power. Also, with the increase in entropy, the amount of heat that must be removed in the condenser increases. Losses similar to those in the turbine also occur in the pump, where the increase in entropy during the compression of the liquid increases the work required to drive the pump. Other significant losses include pressure losses caused by friction and heat leakage into the surroundings as the working fluid flows through the pipes, boiler (steam generator), and condenser.” A comparison of the ideal and real cycles is shown in the next diagram.
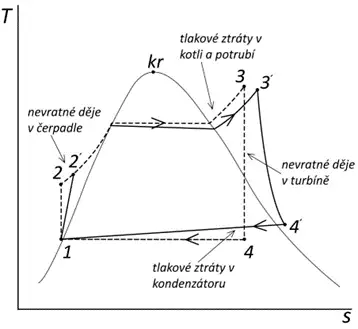
To increase thermal efficiency (T. HORÁK) presents two possibilities: reducing the pressure in the condenser and changing the pressure and temperature of the steam. These depend on the price and quality of technologies, equipment construction, and the quality and price of the fuel.
Common pressure in condensers typically ranges from 2.5 kPa to 9 kPa, depending on the fuel price, and for nuclear power plants, it ranges from 8 to 9 kPa, meaning nuclear fuel is considered inexpensive from this perspective. The pressure and temperature of the steam cannot be freely adjusted due to material limitations.
For highly alloyed austenitic materials, the temperature in fossil fuel units has stabilized at 550°C, but these materials have several drawbacks, such as high cost, poor thermal conductivity, and high thermal expansion.
“For nuclear power plants, the pressure and temperature of the steam are limited by the type of reactor used and its coolant. The design of most nuclear reactors does not allow for superheating of steam; they only produce saturated steam with temperatures ranging around 280-290°C.”
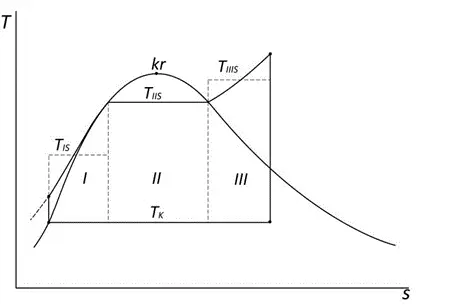
During carnotization, the Rankin-Clausius cycle is divided into three parts (see figure): I – heating of compressed water to saturated liquid; II – heating of saturated liquid to saturated steam; III – superheating of steam.
The efficiency of the Carnot cycle depends only on the temperatures between which it operates. The lowest efficiency occurs in region I of the Carnot cycle, which we try to improve through heat regeneration. “Heat regeneration aims to reduce, ideally eliminate, region I, where heat is added to the working fluid at the lowest temperature, thereby reducing the impact of this region on the overall thermal efficiency of the cycle. Heat regeneration is carried out by controlled extraction of steam, most often after expansion in the high-pressure part of the turbine. After steam expansion in the high-pressure turbine, part of the steam is extracted and fed into a heater (regenerative heat exchanger), where the steam transfers heat to the feedwater before it is heated by the reactor heat. The regenerative steam in the heater condenses, and the resulting condensate is diverted to the condenser.” “The resulting thermal efficiency of the cycle is higher; by reducing region I, the mean temperature at which heat is added to the cycle increases. This is known as carnotization of the cycle.”8.
To improve the efficiency of region III, steam reheating is used. “In nuclear power plants, steam reheating is difficult to achieve. In a single-loop arrangement of a nuclear power plant, where the turbine operates with radioactive steam, reheating is not used due to the problem of heater placement. In two- and three-loop arrangements, steam reheating is done in several ways. In gas- and liquid-metal-cooled reactors, reheating is done by primary coolant in a separate heat exchanger or in a steam generator with an embedded reheater. In PWR reactors, steam reheating is mainly done using the input steam to the turbine or steam extracted from the turbine. However, with this method of reheating, steam cannot be heated to a temperature higher than the saturation temperature corresponding to the pressure of the input steam. Reheating is usually accompanied by separation of excess moisture in the separator. The main reason for reheating saturated steam remains the necessity of ensuring the dryness of the steam after expansion.”9.
Nuclear power plants use reactors with an active zone, where a controlled fission chain reaction occurs. The fission in the entire volume of fuel heats the fuel, and the nuclear energy bound in it is converted to thermal energy. Electrical energy production then occurs using the Rankin-Clausius cycle, or in some cases, using the Brayton cycle in gas-cooled reactors. The thermal power of the active zone is primarily limited by the thermal power that can be extracted from the active zone of the reactor (not theoretically limited by neutron flux). From a thermodynamic perspective, the most interesting aspects are the reactor design, the configuration and cooling of its active zone, the type and parameters of the coolant, and possibly the overall concept of the nuclear power plant, as shown in the next figure.
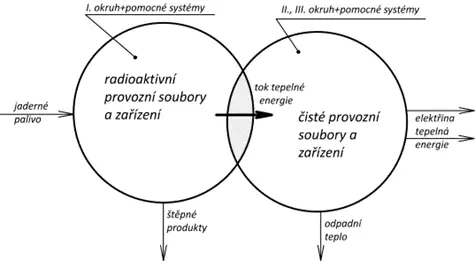
„Especially due to the potential risk of radioactive leakage, or due to the specific design of the reactor, the heat generated in the active zone cannot be directly used for steam or gas heating or for driving a steam or possibly gas turbine. It is necessary to structurally separate the equipment and operational units that may come into direct contact with radioactivity or be affected by it, from equipment that must not come into contact with radioactivity. Therefore, the layout of nuclear power plants is generally multi-loop, with a closed primary circuit containing radioactive coolant that mainly only carries heat away from the reactor and transfers it to other thermal circuits. Nuclear power plants can be divided into three groups – single-loop, double-loop, and triple-loop nuclear power plants.“
Due to the aforementioned reasons, the work further describes the different types of reactors and technical solutions for circuits. Another outcome of the work is the description of a program for plotting and calculating the Rankin-Clausius cycle in MATLAB.
In conclusion, the work reflects on energy trends and the attitudes of certain countries towards nuclear energy, as well as the current efficiency of replacing nuclear power with renewable energy sources. The author acknowledges the potential and applicability of using smaller nuclear reactors for individual technological units or for supplying electricity to smaller residential units or cities. As already mentioned, the work does not focus on extreme events that may occur in nuclear power plants due to external and internal faults, but from a comprehensive perspective on technologies and the use of thermodynamics, it is clear that these are devices that operate with high thermodynamic parameters, and the safety of operation with respect to the thermodynamic processes occurring inside is highly sensitive to the quality of materials, technological solutions, and the organization of construction, operation, etc.
Finally, to illustrate the importance of thermodynamics in nuclear energy safety, we recommend the following videos: